In the early 21st century, the world has witnessed the rise of several transformative technologies—artificial intelligence, biotechnology, and renewable energy, to name a few. But among these emerging domains, quantum technology stands out not only for its scientific depth but also for its profound potential to redefine computing, communication, and sensing. As this industry matures and begins to transition from laboratory research into deployable, scalable hardware systems, it is bringing with it an unexpectedly acute and specialized need: a dramatically increasing demand for precision machined parts.
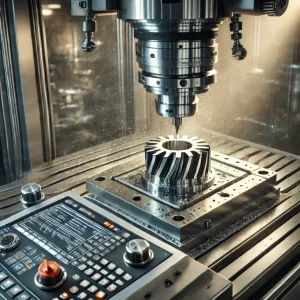
This demand is not incidental. It is rooted in the very nature of quantum systems themselves. Unlike classical electronics, which can tolerate a fair amount of thermal noise, mechanical imprecision, and material variability, quantum systems are extraordinarily sensitive. The phenomena that underpin their functionality—coherence, superposition, entanglement—are easily disrupted by even the slightest environmental interference. Mechanical vibration, thermal fluctuation, electromagnetic fields, or even microscopic inconsistencies in geometry can destabilize these quantum states, rendering a system inoperative or, at best, unreliable.
To safeguard and control quantum phenomena in real-world conditions, hardware must be engineered with extreme accuracy. Every aspect of the system, from the cryogenic enclosures that maintain superconducting temperatures to the optical pathways that guide single photons with nanometer precision, must be built to the highest standard of mechanical integrity. And this is where the precision machining industry enters the equation—not as an auxiliary function, but as a cornerstone of quantum progress.
At its core, the quantum industry encompasses several major application areas: quantum computing, quantum communication, quantum sensing, and quantum metrology. Each of these domains involves unique hardware requirements, but they all share one trait in common—they rely on physical systems that are highly complex, extremely compact, and intolerant of error. Whether it’s the frame that supports an ion trap, the optical housing that maintains laser alignment in a photonic chip, or the vacuum-compatible component that channels signals inside a cryostat, each part must be machined with sub-micron precision and made from carefully selected materials that won’t introduce magnetic noise, outgassing, or structural instability.
This environment is vastly different from typical commercial or industrial settings. Quantum systems are not plug-and-play devices. They are deeply integrated systems where software, electronics, thermal dynamics, and mechanical design must all work in concert at astonishing levels of fidelity. Small flaws in design or fabrication—such as an off-center bore, a slightly rough surface finish, or a material impurity—can cause quantum bits (qubits) to decohere prematurely or render signal transmission inconsistent. These constraints place tremendous pressure on hardware developers to source and fabricate mechanical parts that meet specifications rarely required in traditional industries.
The complexity of quantum hardware has also outpaced the capabilities of many conventional manufacturing workflows. Traditional casting, forging, or even general-purpose CNC machining often cannot achieve the tolerances or cleanliness levels necessary for quantum systems. In response, the industry has increasingly turned to ultra-precision machining, leveraging advanced 5-axis CNC systems, Swiss-type lathes, wire EDM, and even hybrid subtractive-additive techniques to create bespoke parts that meet the stringent demands of quantum environments. These components are often one-of-a-kind or produced in small batches, especially during the research and prototyping phases, which further elevates the role of highly adaptable, design-responsive precision manufacturing.
In addition to geometric precision, material performance is a driving factor behind this surge in demand. Quantum hardware often requires materials that exhibit specific electrical, thermal, and magnetic properties. For example, dilution refrigerators used in superconducting quantum computers rely on parts made from oxygen-free high-conductivity (OFHC) copper due to its excellent thermal and electrical characteristics. Similarly, ion traps may use titanium or ceramic parts to ensure non-magnetic behavior and chemical inertness. These materials are notoriously difficult to machine and require specialized tooling, handling, and finishing processes to avoid deformation, surface damage, or contamination. Precision machining shops equipped with the expertise and tools to process such materials are becoming essential partners in the quantum supply chain.
Compounding this challenge is the trend toward system miniaturization and modular integration. As quantum systems evolve toward commercial viability, they must become smaller, more portable, and more robust. This demands intricate mechanical designs that integrate multiple functions into compact spaces—alignment systems, shielding enclosures, heat sinks, waveguides, and connectors—all within the footprint of a desktop device or smaller. Achieving this level of integration requires not just cutting-edge design, but machining capabilities that can execute those designs in reality with minimal iteration or margin for error.
There is also an increasing emphasis on repeatability and scale. The quantum industry is at an inflection point where early research is giving way to pilot manufacturing. Startups and institutional labs that once relied on handcrafted or manually assembled prototypes are now looking to produce dozens or even hundreds of units for testing, deployment, and partnership validation. This shift demands precision machining workflows that are not only accurate but also repeatable, traceable, and capable of maintaining quality across larger batches. It’s not enough to produce a single perfect part; manufacturers must be able to produce a consistent run of them, each matching the next to the micron.
This trend has created a bottleneck in the quantum hardware ecosystem. The demand for ultra-precise mechanical parts is rising faster than many machining shops can adapt to it, especially in regions where quantum technology is advancing rapidly. This has led some quantum hardware firms to invest in in-house machining capabilities or to form long-term partnerships with specialized machine shops that can co-develop component designs and refine manufacturing techniques in parallel with R&D. The machining industry itself is evolving in response, with forward-thinking suppliers dedicating teams, equipment, and cleanroom facilities to serve the unique needs of quantum customers.
Moreover, this demand extends beyond mere manufacturing—it is increasingly about collaboration and co-innovation. Quantum hardware developers are turning to machinists not just as vendors, but as design partners. The most successful relationships are those where mechanical engineers and quantum physicists work side by side, refining designs not only for performance but also for manufacturability, cost-efficiency, and scalability. These collaborative efforts are driving innovation in materials science, machining processes, and assembly techniques, leading to new manufacturing paradigms tailor-made for the quantum era.
In essence, the quantum industry is pushing the boundaries of what precision machining can achieve. It is compelling manufacturers to develop new capabilities, adopt higher standards, and invest in technologies that can produce components that function at the limits of physical possibility. This relationship is not temporary or transitional—it is foundational. As quantum technologies move from prototype to platform, from laboratory to market, the demand for advanced, reliable, and precision-machined parts will only intensify.
In the coming years, quantum computers may solve problems in hours that would take classical supercomputers millennia. Quantum sensors could revolutionize medicine, geology, and navigation. Quantum communication networks might protect global data from even the most sophisticated cyberattacks. But none of this will happen without the silent, indispensable work of the machinists, engineers, and manufacturers who turn blueprints into reality—who build, with atomic precision, the physical machinery of the quantum world.
That is why the quantum industry is not just influencing the world of precision machining—it is reshaping it, elevating it to a new level of importance, and driving a demand that is truly unprecedented. The partnership between quantum visionaries and the craftsmen who give their ideas form is not just essential—it is the foundation upon which the entire future of quantum technology rests.