As humanity stands at the threshold of the next great technological revolution, quantum technology is quickly evolving from the realm of theoretical physics into a real-world industry poised to reshape computing, communication, sensing, and security. Governments and private enterprises around the globe are investing billions into the quantum frontier, fueling innovation at a pace rarely seen in advanced research domains. But behind the groundbreaking scientific theories and complex quantum algorithms lies a crucial, often underappreciated enabler of this transformation: CNC machining.
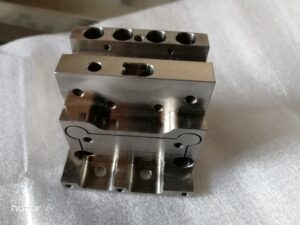
Precision engineering has always played a pivotal role in scientific advancement. In the case of the quantum industry chain, the importance of ultra-precise mechanical components cannot be overstated. Quantum systems are, by nature, delicate and extremely sensitive to external variables such as temperature, vibration, electromagnetic fields, and even the smallest physical misalignments. The challenge of creating stable, scalable quantum devices thus depends as much on robust mechanical infrastructure as it does on theoretical design. Here is where Computer Numerical Control (CNC) machining proves itself indispensable—not just as a support function, but as a critical force in accelerating the development, prototyping, and industrialization of quantum technologies.
At the heart of CNC machining’s value to the quantum industry is its unparalleled precision. Quantum computers, for example, require cryogenic environments that maintain qubits in coherent quantum states at temperatures approaching absolute zero. The dilution refrigerators and cryostats that house these quantum processors are built from multiple layers of intricately machined components, including thermal shields, RF-tight enclosures, and mechanical support structures that must maintain structural integrity through extreme thermal cycling. Even a minute deviation in part geometry could compromise the vacuum seal, alter thermal conductivity, or introduce mechanical noise—each of which could render a quantum experiment or system unreliable.
CNC machining enables engineers to meet the extreme tolerances demanded by these systems, often achieving sub-micron precision and surface finishes that minimize unwanted heat transfer, light reflection, or electromagnetic leakage. This level of consistency and exactness allows researchers and developers to focus on optimizing qubit design and control electronics without being hampered by unpredictable mechanical behavior. In essence, CNC machining provides the physical reliability that quantum systems need to explore the edge of theoretical possibility.
As the industry moves from laboratory setups to deployable quantum devices, the speed of iteration becomes just as vital as precision. CNC machining facilitates rapid prototyping with extremely short lead times. Engineers working on new cavity designs for superconducting qubits or novel housing structures for trapped-ion chips can quickly translate CAD models into physical parts using CNC workflows. Unlike injection molding or casting, which require expensive tooling and long preparation times, CNC machining can turn out one-off or small-batch parts quickly and with full geometric fidelity. This ability to rapidly test and refine mechanical designs accelerates the entire R&D cycle, allowing breakthroughs to be verified, validated, and prepared for scaling at an unprecedented pace.
Moreover, CNC machining’s role in accelerating the quantum industry chain is not confined to computing alone. Quantum sensing devices, which are being developed for applications ranging from subterranean navigation to biomedical imaging, also rely on mechanically stable, precisely aligned assemblies. These devices often integrate optical, electrical, and magnetic subsystems in compact housings that must maintain strict dimensional relationships. CNC machining provides the necessary control to produce mounts, enclosures, and alignment features that ensure sensor fidelity and long-term stability—crucial for real-world deployment outside controlled laboratory settings.
In quantum communications, where photons are used to transmit data through fiber or free-space channels, CNC-machined components are used to house and align lasers, modulators, beam splitters, and detectors with sub-millimeter accuracy. The physical layout of these components can affect loss rates, signal integrity, and timing accuracy. With the growth of global initiatives to establish quantum communication networks and quantum key distribution (QKD) systems, the need for scalable, reproducible, and miniaturized optical-mechanical assemblies is becoming urgent. CNC machining is one of the only methods capable of producing such components reliably, efficiently, and to the demanding tolerances required for secure quantum links.
One of the greatest advantages of CNC machining in the context of quantum hardware development is its material versatility. Quantum systems often require components made from non-magnetic, non-reactive, or cryogenically stable materials such as titanium, copper, OFHC (oxygen-free high-conductivity) copper, Invar, Macor ceramic, and various grades of stainless steel. These materials can be difficult to machine without specialized knowledge, equipment, and tooling. However, CNC machining—especially when operated by experienced machinists familiar with the needs of scientific equipment—can consistently produce parts from these materials without compromising structural or material properties. This capability ensures that parts perform correctly not just mechanically, but thermally and electromagnetically as well—factors that are critical in quantum systems.
Beyond the physical characteristics of parts, CNC machining also plays an essential role in developing the infrastructure required for mass production. As quantum technologies mature, they must transition from laboratory setups to industrial-scale systems with mass-produced, interchangeable components. CNC machining’s automation, digital integration, and repeatability make it ideal for this transition. CAM (Computer-Aided Manufacturing) systems and CAD (Computer-Aided Design) files allow precise control and replication across machines and facilities, enabling companies to scale production while maintaining tight quality control. This creates the foundation for a robust quantum hardware supply chain, which is essential to meeting the anticipated demand for quantum systems in the coming decades.
Importantly, CNC machining also contributes to sustainability and process optimization within the quantum hardware ecosystem. Compared to other manufacturing methods, CNC machining generates less material waste when optimized for efficient toolpaths and can be paired with recycled or sustainably sourced raw materials. This aligns well with the ethos of quantum technologies, which often promise energy efficiency and reduced environmental impact in computing and sensing applications. By ensuring that the hardware behind these innovations is produced responsibly and efficiently, CNC machining supports not just the advancement of quantum science, but also the sustainability values that often accompany it.
Perhaps one of the most compelling aspects of CNC machining’s contribution to the quantum industry chain is its capacity to bridge research and industry. Many of the breakthroughs in quantum technologies originate in academic institutions, where budgets are tight and production volumes are low. CNC machining allows these institutions to build custom, one-off parts quickly and affordably, enabling experiments that would otherwise be too costly or time-consuming. As these ideas mature and spin out into startups and commercial ventures, the same CNC capabilities can be used to scale production with minimal redesign. This continuity helps preserve intellectual property, accelerate commercialization, and maintain the fidelity of the original research vision.
Looking ahead, as quantum technologies begin to solve problems previously considered intractable—such as simulating molecular interactions for drug discovery, optimizing global logistics, or securing communications against cyberattacks—the need for hardware capable of sustaining quantum operations will only increase. CNC machining, with its combination of precision, flexibility, and scalability, will remain at the core of this infrastructure. It will not only provide the physical parts that house, connect, and protect quantum components but also the manufacturing speed needed to keep up with the rapid pace of discovery and deployment.
In this way, CNC machining is far more than a background process in the quantum age. It is a key accelerator, a driver of innovation, and an essential link in the quantum industry chain. Without it, the future of quantum technology would remain largely theoretical. With it, that future is being built—accurately, efficiently, and at scale.