In today’s competitive manufacturing landscape, precision and efficiency are critical factors for success. The advent of 4-axis CNC (Computer Numerical Control) machining has significantly contributed to advancements in complex part production, offering improved accuracy, faster production times, and increased capabilities. A 4-axis CNC machining service factory specializes in providing high-quality machining services that cater to industries such as aerospace, automotive, electronics, and medical equipment, where complex parts are often required.
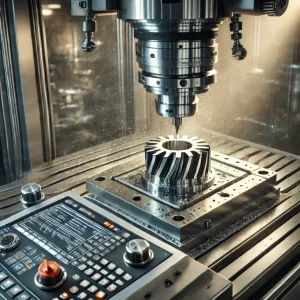
What is 4-Axis CNC Machining?
A 4-axis CNC machine is an advanced type of milling machine capable of moving a cutting tool or workpiece along four different axes. In addition to the standard X, Y, and Z axes that allow for horizontal, vertical, and depth movements, a 4-axis machine incorporates a rotational axis, known as the A-axis. This rotational axis enables the machine to rotate the workpiece around the X-axis, allowing for complex operations without the need for manual repositioning.
The additional axis makes it possible to perform multiple cuts on different surfaces of the workpiece in a single setup, which is a key benefit over traditional 3-axis machining. This increases both the speed and precision of the manufacturing process, reducing the need for multiple setups and enhancing overall productivity.
Benefits of 4-Axis CNC Machining
- Improved Precision and Complexity
4-axis CNC machining allows for the production of intricate parts with greater accuracy. Complex geometries, undercuts, and curves that are difficult or impossible to machine using traditional methods can be easily achieved with this technology. This is especially important in industries like aerospace, where precision and tolerance are critical. - Higher Production Efficiency
By enabling multiple operations on different sides of a workpiece without the need for repositioning, 4-axis machining reduces the time spent on setup and human intervention. This not only saves time but also minimizes errors associated with manual handling, improving overall efficiency and output. - Versatility Across Industries
A 4-axis CNC machining service factory can cater to various industries with diverse needs. Whether it’s producing custom parts for the medical industry, intricate components for electronics, or high-performance automotive parts, 4-axis CNC machines offer flexibility and adaptability to meet different design and material specifications. - Cost-Effectiveness
While the initial investment in a 4-axis CNC machine may be higher, the long-term cost benefits are significant. Reduced production time, fewer errors, and less waste contribute to a lower overall cost per part, making this an attractive option for businesses seeking cost-efficient manufacturing solutions.
Services Offered by a 4-Axis CNC Machining Factory
A specialized 4-axis CNC machining service factory offers a range of services that cater to the diverse needs of clients, including:
- Custom Part Production: Factories work with clients to create custom parts based on their designs. These services are often used in industries such as robotics, consumer electronics, and medical devices, where unique components are needed.
- Prototyping and Small Batch Production: CNC machining services are ideal for creating prototypes or small batch runs of products. With 4-axis machining, companies can quickly and accurately produce prototypes that closely match the final design.
- Precision Machining for Aerospace and Automotive Industries: Industries that require high-precision parts rely heavily on 4-axis CNC machining. Factories can produce lightweight, durable parts for aerospace, automotive engines, and suspension systems.
- Post-Processing Services: Many 4-axis CNC machining factories also offer secondary services like anodizing, powder coating, or polishing to ensure the finished product meets industry-specific standards for quality and durability.
Key Considerations When Choosing a 4-Axis CNC Machining Service Factory
When selecting a 4-axis CNC machining service provider, it’s important to evaluate several factors:
- Technical Expertise: Look for a factory with skilled technicians and engineers experienced in operating advanced CNC machinery. Expertise ensures that projects are completed efficiently and meet exact specifications.
- Quality Control: A reputable CNC machining factory should have stringent quality control measures in place to ensure that all parts meet industry standards and customer expectations. Inspection tools like coordinate measuring machines (CMM) are often used to ensure accuracy.
- Materials and Capabilities: Ensure the factory has experience working with a range of materials, including metals, plastics, and composites. The ability to machine different materials expands the versatility of the services they can offer.
- Lead Time and Flexibility: Time-sensitive projects require a factory that can meet tight deadlines without compromising on quality. Inquire about the factory’s production capacity and ability to handle rush orders if necessary.
The Future of 4-Axis CNC Machining
With the ongoing development of CNC technology, the future of 4-axis machining is promising. Innovations like advanced software, automation, and real-time monitoring systems are making CNC machines more efficient and easier to operate. As demand for high-precision components grows across various industries, 4-axis CNC machining service factories will continue to play a pivotal role in shaping modern manufacturing.
In conclusion, a 4-axis CNC machining service factory offers an indispensable service for companies looking to create high-precision, complex parts with speed and efficiency. As technology evolves, these factories are poised to provide even more versatile and cost-effective solutions, driving innovation in fields ranging from aerospace to consumer electronics.