Feed Rates
At the point when any feed-type move is modified, a feed rate should be allotted to it. Feed rates are modular and assuming none is modified in a square, the recently customized rate will in any case be dynamic. A F-character relegates the ideal feed rate.
Feed rates can be communicated in either inches each moment (IPM), utilizing a G94 code, or inches per upset (PR), utilizing a G95 code. This is regularly set at the outset segment of the CNC program or on the protected beginning square, yet can be actuated or changed whenever in the program. For processing tasks, utilization of IPM is generally normal, however IPR is here and there utilized for holemaking activities.
Feed unit settings are likewise modular, so consistently make certain of the setting that is dynamic. On the off chance that the machine is in G94 (IPM) and a feed pace of F.005 is customized (a satisfactory feed for IPR), the hub will move at just 0.005 inches each moment. In the event that the machine is in G95 (IPR) and F40.0 is customized (an adequate feed for IPM), the machine will move at 40 inches for each shaft insurgency!
An illustration of a quick situating move followed by two consecutive straight moves in a program seems as though this (notice the absence of G1 code in the last square, since it is now modular):
Roundabout Interpolation
Roundabout shaper ways can be made utilizing roundabout introduction. This movement can be utilized by china precision parts factory to process part highlights, for example, corner radi, bends, and round pockets.
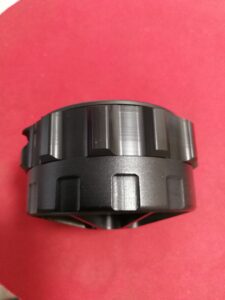
To program a curve development, the instrument should initially be situated at the beginning stage of the bend. At that point a G-code is utilized to show either clockwise or counterclockwise development. A G2 order is utilized for clockwise movement, and a G3 order is utilized for counterclockwise movement.
China precision machined components suppliers illustrates an illustration of a G2 and a G3 development.
In the very square that the G2 or G3 code is given, the software engineer should likewise distinguish the end point where the curve is to stop (recollect that the device was at that point toward the beginning point before the roundabout interjection order). A G2 order and a bend end point is added to the last model and featured underneath:
G0 X1. Y1. (Quick X AND Y TO START POSITION);
G1 Z-.1 F15. (Direct FEED Z TO DEPTH)
X-1.5 F30. (Straight FEED X TO NEXT POSITION);
G2 X-2. Y1.5 (CW ARC MOVE TO NEXT POSITION);
Be that as it may, this is as yet insufficient data for a round insertion move. The control realizes the beginning point, the end point, and the heading, however there is no data about the size of the circular segment span. See Figure 8.6.5 for an ilustration of why the sweep data is required. The very square of code that enacted round interjection should likewise contain that sweep data. There are two strategies for programming the size of the sweep: the bend place technique and the span strategy. The bend community technique has the upside of having the option to cut a 360-degree circular segment (round trip) utilizing just one line of code, where the sweep strategy requires round trips to be broken into two pieces and customized with two squares of code. The R-technique is generally simpler for another developer to see, nonetheless. This article is from